Maximizing Efficiency: Building a business case for a Downtime Tracking System
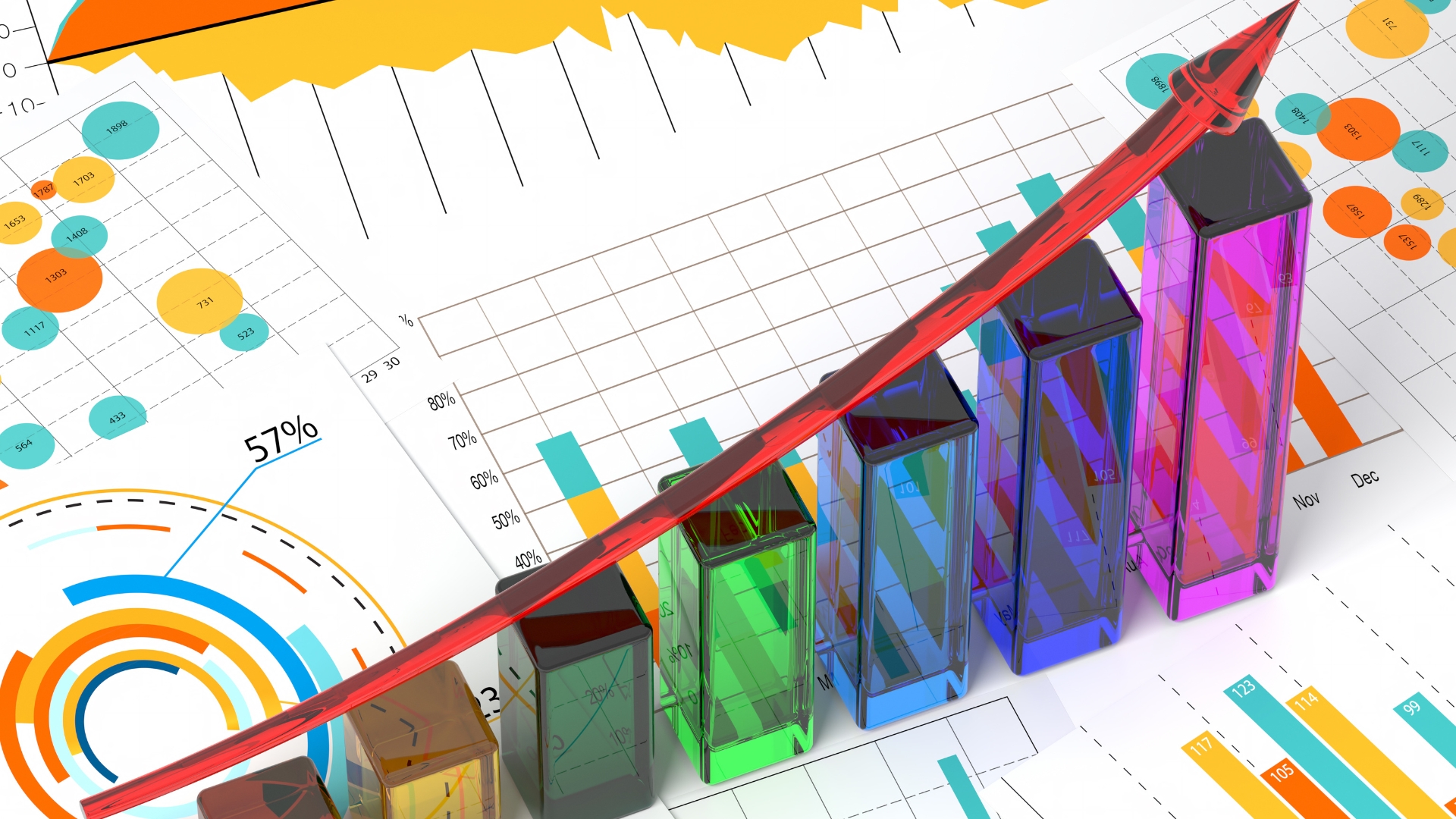
When it comes to manufacturing operations, unscheduled downtime and delays can lead to significant production chain losses. Not only does it result in lost capacity and production opportunity it also drives increased maintenance cost. A survey found that 81% of organizations believe that digital tools play a significant role in reducing unplanned downtime. Implementing a downtime system is the first step to gaining a better understanding of your operations and figuring out the root cause of lost capacity. This article examines the methods for justifying the implementation of downtime tracking systems.
Building the business case for a downtime tracking system
A robust downtime tracking system is critical for improving the productivity of your operation and driving down cost. Any investment is subjected to a project evaluation to ensure the expected benefits outweigh the costs. However, as with many data management projects, the investment in a downtime tracking solution doesn’t necessarily directly result in a return on your investment. Rather, tools like this are an enabler for operations to more efficiently gather and manage their data and ultimately use that data to identify improvements in their business.
The following three business cases can be used to underpin the development of a project authorization request.
An increase in running time
A typical way to quantify the value of a downtime tracking system is to predict the future increase in production time by implementing improvements uncovered by analyzing the downtime tracking data. Since the value of operating time varies from plant to plant, each business case needs to use the specific operating metrics for that plant.
Imagine a plant whose production rate is 500 tph and net product value is $45 per ton. An increase from 90% to 91% running time would result in almost $2 million more in annual revenue for that plant. This 1% operating time improvement is derived from the analysis of downtime data captured by an automated system.
A real-life example of this is a manufacturer who analyzed the data captured by their downtime system and found that operator breaks were taking on average 4 minutes longer than budgeted, resulting in an extra 8 hours of downtime per month. They were able to implement a breakroom countdown timer and reduce the average line stoppage due to breaks, which more than covered the cost of the downtime tracking system in the first 4 months.
An increase in production rate
Many operations track downtime events, but few also track when production rates fall below budgeted rates. This is due to the complexity of determining deviation in rates and the resulting productivity loss. Automated downtime tracking systems can be configured to trigger “slowdown” events based on actual and expected production rates. These systems then calculate the equivalent downtime so that slowdown events can be compared to downtime events in terms of lost production opportunity.
To calculate the benefit from increased production rates, the formula Production Rate Increase x Net Product Value x hours in a year x Running Time % can be used. RtTech‘s experience suggests that capturing 15-25% of the available rate opportunity is a typical performance improvement.
For example, a plant with a budgeted rate of 500 tons per hour has an actual average rate of 476 tons per hour, leaving an available rate opportunity of 24 tons per hour. An increase of 4 tons per hour (476 to 480) would have an approximate annual value of $1.4 M using the net product value of $45 per ton from our last example.
Slowdown event tracking provides a new data set for many operations who currently find it too complex or cumbersome to track. Capturing it through an automated system and analyzing the results can very quickly yield an improvement in asset productivity.
Improved Staff Utilization
A downtime tracking system can bring both direct and indirect benefits. The two business cases we’ve discussed are indirect benefits with the ability to uncover opportunities for increased running time and production rates. These benefits are realized because of the analysis of downtime data and implementation of solutions derived from this analysis.
A direct benefit is the improved utilization of technical and operations resources to do more value-added activities, such as analysis and process improvement, rather than spending time on data management tasks. With manual and home-grown systems, the effort required to record, manage, and report on downtime and slowdown events can be substantial. This can lead to a sacrifice in the quantity or quality of downtime data.
A downtime tracking system automates much of the data management tasks, which can lead to a reduction in the time spent managing downtime tracking systems. This can be quantified by measuring the time spent recording, managing, reporting, and cleaning downtime data, which can determine the potential savings in labor hours.
We typically see a reduction in technical staff effort of 8 hours per week to 1 hour per week and operating staff effort of 15 hours per week to 3 hours per week after implementing a downtime system, resulting in nearly 1000-manhour savings per year.
In conclusion, implementing a downtime system is vital for gaining insight into operations and identifying the root causes of lost capacity. Developing a business case can be difficult with any enabler project like a downtime tracking system. Focusing on the potential benefits stemming from the subsequent data analysis in terms of increased running time and throughput is usually the easiest path. However, the reduced effort from technical and operating staff to produce the datasets and reports should not be ignored.
-Written by Matt Lindsay, Client Manager of RtTech Software.