What are safety audits, and how often should they be performed?
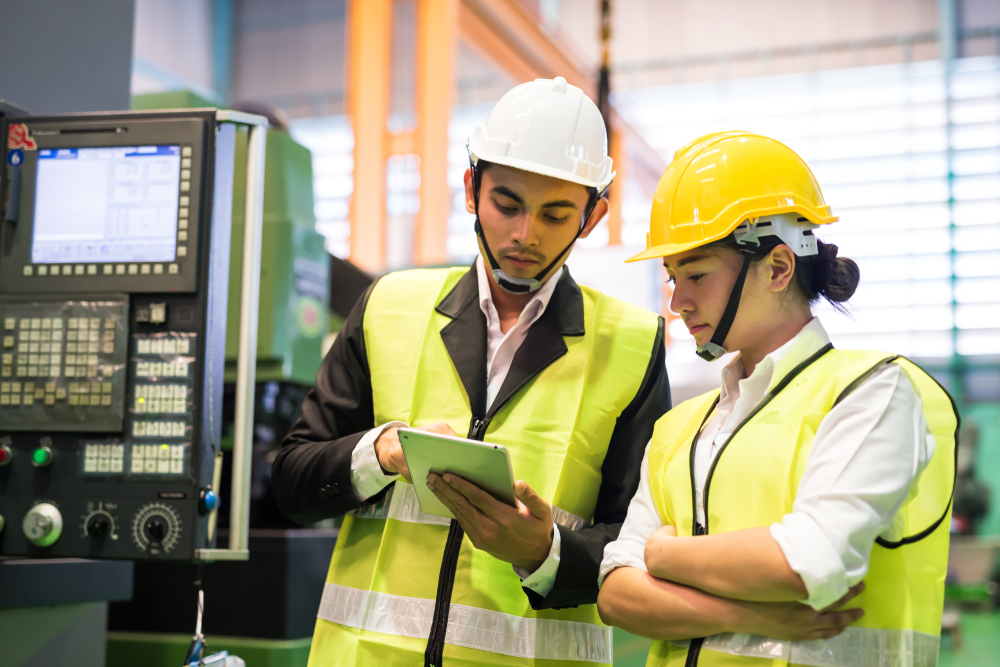
In 2020 alone, Canadian worker’s compensation boards reported that 924 workers died from work-related causes. In Nova Scotia during that same year, there were 516 serious injuries in the manufacturing sector, a number which made up almost 11% of all serious injuries in the province. Workplace safety is no joke. It remains a serious issue which necessitates care, respect, and attention to keep workers safe.
It is the responsibility of all employers to act diligently, by working to ensure that all employees are given the necessary information, training, and supervision so that they can perform their jobs safely. Beyond that, employers must also ensure that all machinery and equipment that their employees use is also safe and functioning as intended. Employees in any given facility also have the right to be informed of known or perceived hazards in their workplace. All these factors contribute to a safe working environment.
Safety must be taken seriously, and, for companies, the smart choice is always to invest in strict, regular safety audits that verify the safety of their workers.
When should safety audits be performed?
At Actemium, we always recommend that internal safety audits are continuously carried out. Equipment, and the ways in which workers use it are everchanging. It is essential that any changes are monitored, and safety of both machines and operators are maintained throughout time. Safety audits will reveal deficiencies present in existing safety protocols, and this information can then be used to address safety concerns and keep workers safe. Any manufacturing plant should schedule and perform regular safety audits to ensure that the various teams of workers interacting with equipment are cared for. Safety is always changing, with devices and procedures being improved and refined constantly. As a company overseeing a manufacturing plant, you must stay up to date on safety developments, whether they be devices, procedures, or technologies, which could improve the safety of existing systems. Although they’re an essential part of maintaining a safe work environment, internal safety audits can suffer since they lack fresh perspective of a plant’s systems and procedures. Incorporating third-party safety audits can assist with Risk Assessment and Hazards Analysis which can identify safety risks that familiar personnel may take for granted.
Essentially, internal audits can reveal the need for an external, professional safety audit. Once a company has internally identified that a machine represents a safety risk, that is the moment external experts should be brought in to address the issue.
How is risk determined?
Multiple aspects of the manufacturing process can be harmful to workers. A sharp edge on a tool, or a large machine press can present risks to employees, and the severity of the risk must be assessed. Severity is determined by assessing the potential for exposure, the frequency of exposure, and the duration of exposure. Once a hazard has been identified, then the risk can be accurately measured.
A common example of a methodology which protects personnel from hazardous equipment is machine guarding. In essence, machine guarding comprises physical barriers installed around machines which protect users from hazards. Industrial machinery commonly makes use of machine guarding, which can protect workers from debris ejected during operation, for example. Machine guarding can also be an effective method for preventing contact with potentially dangerous moving parts or high temperature machine components.
What does the safety audit process look like?
Once a machine is suspected to be hazardous or has been identified as hazardous due to an internal audit, industrial automation companies like ours will get involved. First, we interview those who regularly use the equipment to get a sense of the issues they feel need to be addressed.
After that, it’s essential to thoroughly examine the machine guarding. Machine guarding is often where issues appear, so an investigation into guarding, as well as electrical and pneumatic controls will quickly identify issues. The most common hazards are one that have been present for a long time and gone unnoticed. Over time, procedures that “have always been done that way” are accepted, when they may still put workers in risk.
Safety audits can also be performed before a machine is purchased or installed, where the customer wants to ensure that the machine builder is addressing the customer’s needs.
Why SIS levels and how they are assigned?
The Safety Instrumentation System works to ensure that in the case of a machine operator encountering hazardous energies in a machine, those energies are safely dissipated and are absent until the operator has left the area. In Canada, different SIS levels are referred to as Performance Levels and range from A (least protective) to E (most protective).
It is exceedingly common for the financial cost of a safe facility to be higher than plant owners and operators anticipate. It is also always cheaper to maintain a safe working environment, than it is to face the Ministry of Labour closing a facility for extended periods of time due to an avoidable injury. Setting aside a significant budget for safety improvements and maintenance, as well as listening to employee concerns and feedback is always worth it in the long run.
Ultimately, safer machines require less training, and will enable simpler resource distribution for the company. If an entire facility operates according to the same safety protocols, it will be easier to get everyone on board, and cultivate a safer, more productive environment.
How to manage risks and hazards?
Of course, it is easy to say that the best safety solutions and procedures are ones which eliminate hazards present in the workplace. Putting this philosophy into practice is the challenge. There is a hierarchy of risk reduction which can help you devise safety procedures:
Inherently Safe Design
- Engineer out the part of the manufacturing process which is causing the hazard. For example, if operators may be exposed to hazards while loading raw materials into a machine, incorporate an automatic loading system which eliminates the potentially hazardous task.
Safeguarding and Complimentary Protective Measures
- Integrate machine guarding and other protective devices to eliminate access to the hazard. For example, if operators may be exposed to a hazard while loading raw materials into a machine, install a light curtain to stop the machine when an operator is loading the raw materials.
Information for Use
- Comprised of signage, training, and PPE. For example, if operators may be exposed to a hazard while loading raw materials into a machine, add a sign indicating the presence of the hazard which instructs operators on how to properly load raw materials.
Safety upgrade projects also allow plant operators the chance to examine other potential areas of improvement. Currently, communication protocols that can work from an ethernet network are incredibly popular. They enable full safety-rated communications without the need for additional dedicated architecture. Auxiliary upgrades such as these ensure the safety and robustness of the system into the future.
How emerging safety technology and procedures impact us?
Just before the COVID-19 pandemic began, there was a widespread industry shift towards IoT solutions. This is usually referred to as “Industry 4.0”. At present, it is limited to companies with higher safety budgets, but these technologies will trickle down to more affordable devices and systems as time goes on. For the safety sector, this means better visibility into the internal logic of controllers and devices, and thus greater control over their functions. For example, whereas before a scanner might only tell you whether something was inside its sensor’s ranger, now it will identify exactly where the object is. This is especially beneficial in robotic and self-guided vehicular applications.
What is the future of your workers’ safety?
Investing in the safety of your workplace and its equipment does necessitate a greater upfront investment of time and money. It is also far and away the best possible choice. Regular internal safety audits always pay off in the long run and incorporating the experience of expert safety consultants will ensure the safety of your facility, equipment, and most importantly, your workers.